What training do manufacturer workers need?
Posted 4 years ago
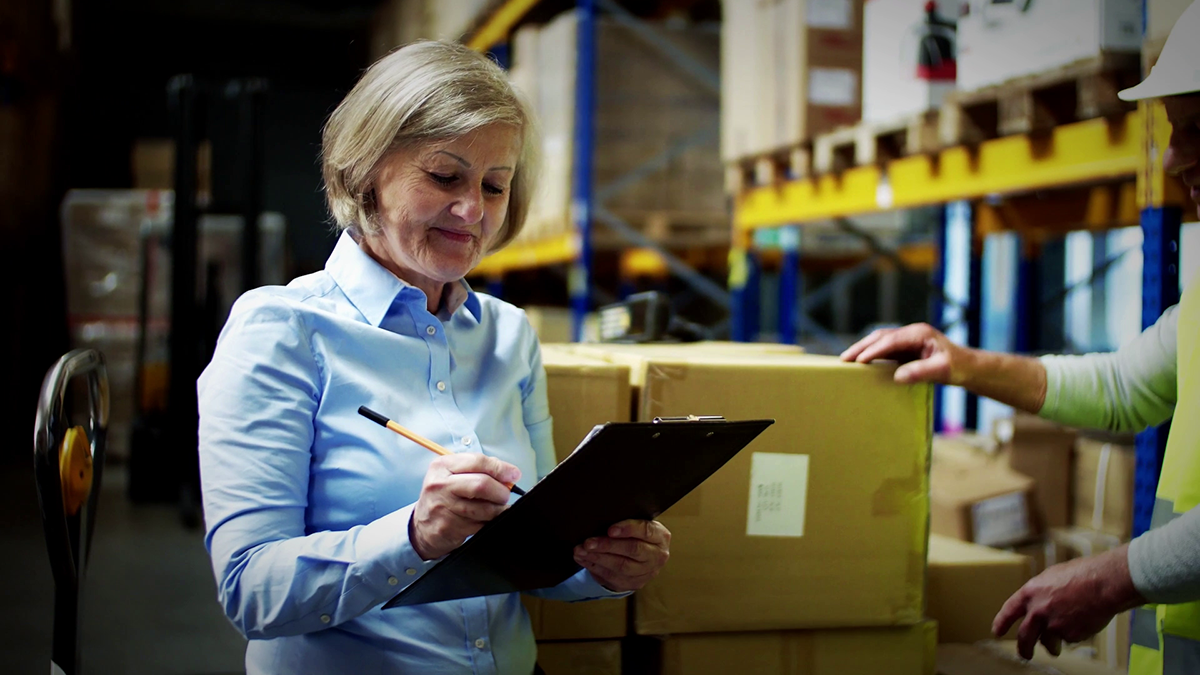
Here at iHasco, we’ve delivered high-quality, engaging eLearning to the manufacturing sector for over a decade, and with over 10,000 clients already benefiting from our training solution, we know a thing or two about workplace training!
However, we understand that figuring out training requirements isn’t always simple. Knowing what staff training is mandatory, figuring out whether all staff require the same training, or deciding on what training each department requires are just some of the things that a manufacturing business may not know the answers to.
With that said, we have put together this guide to help those working in the manufacturing sector gain a better understanding of what training their staff may require.
First steps
The first step businesses should take when sorting out their training needs should always be conducting a risk assessment for each job role. By doing this, organisations can identify any risks that might be associated with a group of employees.
For organisations with five or more employees, it is a legal requirement to have a written risk assessment. They should also have a written Health & Safety policy, which should be shared with all employees to ensure it remains effective.
Learn more about the basics of Health & Safety in your business with the HSE’s Health & Safety made simple guide.
What training is mandatory?
Starting with the courses that are mandatory for all staff is often the most logical way to identify an organisation’s training needs.
All employees are legally required to undertake a form of Health & Safety training. However, there are a number of specific courses staff may need to complete.
Fire Awareness & Warden training
No matter what their role on a site, it is a legal requirement that every employee receives a form of fire safety training, as well as instruction from their employer.
Employers must also provide their appointed members of staff with specialist Fire Warden Training.
Finally, employers should also keep their fire risk assessment up-to-date with regular reviews. This assessment should be shared with all employees to make them aware of any risks that have been identified and to give them the opportunity to raise concerns of risks that may not have yet been identified by the organisation.
DSE (Display Screen Equipment) training
Employees who are required to regularly use display screen equipment (DSE) must be provided with sufficient DSE Training.
Those who aren’t sure about who should be considered as a DSE user can find out more information on our blog.
Manual Handling training
Any employee that may be required to lift, lower, pull, or push objects as part of their work must be provided with manual handling training to help alleviate the risk of injury.
Organisations that are just looking to cover mandatory training can check out our mandatory training bundle.
Other training considerations for manufacturer workers
Other core health & safety
COSHH – Those working in the manufacturing sector often work with substances that are considered hazardous, whether it be a substance in the manufacturing process or the substance being manufactured and packaged itself. It is strongly advised that employees who have to regularly work with hazardous substances should be provided with effective training from their employer.
Slips, Trips, and Falls – Being a relatively high-risk sector, compared to other industries, the manufacturing sector can be more prone to slips, trips, and falls. Training staff to understand how to avoid accidents is a must.
First Aid – All organisations require ‘adequate and appropriate’ first aid provisions, including facilities, equipment, and personnel. First aiders must be provided with adequate training, including face-to-face training every three years, and regular refresher training in between.
Risk Assessment – Where organisations with five or more employees are required to document their risk assessments, they must employ someone who is competent in undertaking the assessment. With effective training, employers can ensure that their dedicated employees undertaking the assessments are competent.
Accident Reporting – Any accidents that occur in the workplace must be recorded, regardless of how big or small they might be, as it is a legal requirement. An organisation’s appointed person should have a great understanding of how to properly report an incident, and what can be done to ensure the incident doesn’t occur again.
Working at Height training – In some instances, employees in the manufacturing sector may have to perform a task whilst working at height. Any person who is required to work from height, and those that are supervising an employee doing so, should be provided with an understanding of their legal responsibilities and best practices when working from height.
Personal Protective Equipment (PPE) – PPE is often used in the manufacturing sector to ensure that employees have an extra layer of protection when performing tasks that might pose risks. All employees required to wear PPE should be given a proper understanding of how to wear it correctly, when they need to wear it, and how to look after it.
LOLER Training – The Lifting Operations and Lifting Equipment Regulations 1998 are in place to ensure that safe lifting operations are carried out to reduce the chance of accidents occuring when lifting. All employees involved in lifting operations should have a complete understanding of their responsibilities under the regulations.
PUWER – The Provision and Use of Work Equipment Regulations 1998 are in place to make organisations ensure their equipment is suitable for use, maintained in a safe condition, and regularly inspected. All employees that are required to use equipment in the workplace should be provided with an understanding of the regulations and their responsibilities.
Eye Protection – It is estimated that roughly 90% of eye injuries could have been avoidable with the correct eye protection. With that said, it is essential that all organisations equip their employees with the information they need to identify hazards and the risk they pose to their eyes in order to avoid accidents from happening.
General Workshop Safety – Anybody who works in a workshop should be provided with information on general safety awareness, safe working habits, and safe operating procedures.
Ladder Safety – Falls from ladders account for roughly 40% of all falls from height. Therefore, it is crucial that employees are provided with instructions on how to use a ladder correctly and how they should comply with the Work at Height Regulations 2005.
Hand Arm Vibration – Although the effects of vibration exposure are irreversible, they can be prevented in the first place. Employees at risk to HAVS should be provided with training to ensure they understand how to reduce exposure to vibrations, their employer’s responsibilities under the Control of Vibration at Work Regulations 2005, and how to recognise early signs of HAVS.
Noise Awareness – There are hundreds of thousands of employees in the UK that suffer from hearing loss as a result of work, and it is crucial that those who are working in loud environments are given an understanding of how to reduce noise and how to prevent hearing loss as a result of noise.
Food Hygiene – Food hygiene training should be given to any person directly involved in a production line that manufactures food. With over one million cases of food poisoning being reported in the UK each year, it is crucial that employees are given an understanding of personal hygiene, cleanliness, food storage & temperatures, and cross-contamination hazards with food, amongst a number of other areas.
Abrasive Wheels – With early half of all accidents involving abrasive wheels occuring because of an unsafe system of work or operator error, it is essential that employees required to use abrasive wheels understand the dangers abrasive wheels pose and how to spot them.
DSEAR – Anyone who works with flammable or potentially explosive substances or substances corrosive to metal should understand that without proper controls in place, these substances can ignite and explode, causing serious harm to anyone nearby. It is essential that employees are provided with thorough training to alleviate the chance of an accident occurring.
HR essentials
Equality, Diversity & Inclusion – Organisations that are more inclusive and diverse likely have better morale, staff retention rates, and reputation compared to those who don’t. There are many ways organisations can be more inclusive and diverse, and providing all employees with training is a great stepping stone.
Disability Awareness – With over 4.1 million disabled people currently in work in the UK, it is very likely that an organisation already employs, or will eventually employ a person with a disability. Employees should be educated to understand the importance of creating and maintaining an inclusive workplace culture, including for those with disabilities.
Bullying & Harassment – Every employee should be able to feel comfortable in their place of work at all times. However, bullying at work can stop employees from feeling safe and comfortable. Therefore, it is essential that all employees understand what is considered bullying and how to report it if identified.
Sexual Harassment Awareness – Roughly 60% of UK adults believe that better training on the topic of sexual harassment would be an effective way of reducing it in the workplace.
Drug & Alcohol Awareness – Roughly 17 million working days are lost each year as a result of alcohol and drug abuse. It is crucial that employees raise awareness of substance abuse, the damage it can cause, how to identify it, and where a person can get help.
Bribery and corruption
Any employees who are required to deal with external suppliers, clients, and other partners could fall victim to bribery or corruption.
Unfortunately, it is often the case that employees get unintentionally caught up in this type of corruption, which is why providing them with the training they need to identify signs of corruption is a must.
Mental health & wellbeing
Employers must ensure that all employees feel they have support when it comes to their wellbeing. One of the best ways to encourage positive wellbeing is to help break the negative stigma surrounding wellbeing in general.
Providing employees with the tools they need to understand and improve their mental health & wellbeing not only allows them to take care of themselves, but also helps them look out for their colleagues.
Soft skills
Soft skills are incredibly important in the modern workplace. In fact, 93% of employees agree that they consider Soft Skills to be either an “essential” or “very important” factor in hiring decisions.
Some key soft skills that benefit the manufacturing sector include:
- Problem solving
- Critical thinking
- Confidence building
- Communication skills
- Conflict resolution
- Customer service
- Mindfulness
Looking for high-quality, cost-effective training?
We support over 10,000 UK clients with our cost-effective and high-quality online training, and many organisations working in the manufacturing sector benefit from our range of course subjects!
Our course library hosts over 140 approved and accredited courses that each provide a printable certificate upon completion.
With our engaging training courses, easy-to-use Learning Management System, and unrivalled customer support, sorting workplace training has never been easier!
But don’t just take our word for it, see why Tate Fencing uses iHasco for their training needs.
You can get started today with instant access to our entire course library! Alternatively, if you’re ready to get started you can request a quote and a member of our team will get in touch with you shortly.
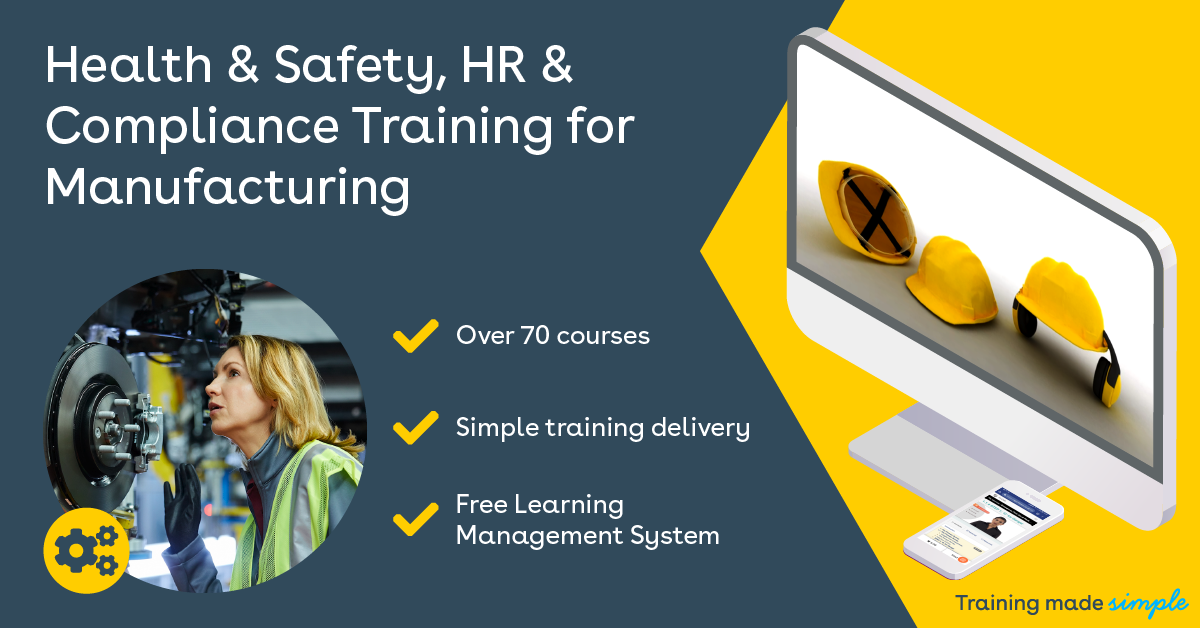
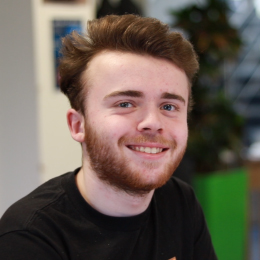
Jack Rosier
Content Executive
Related articles
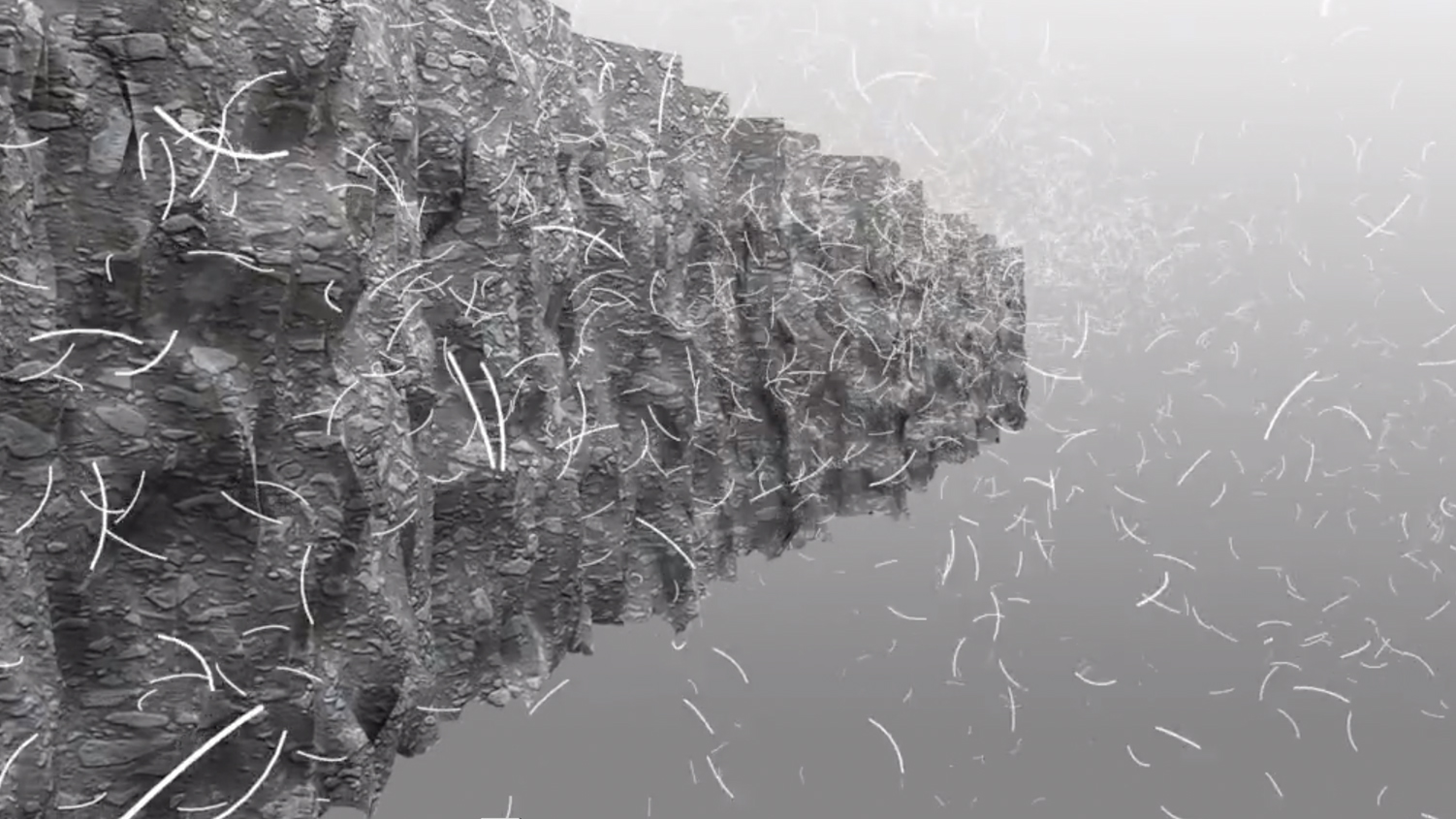
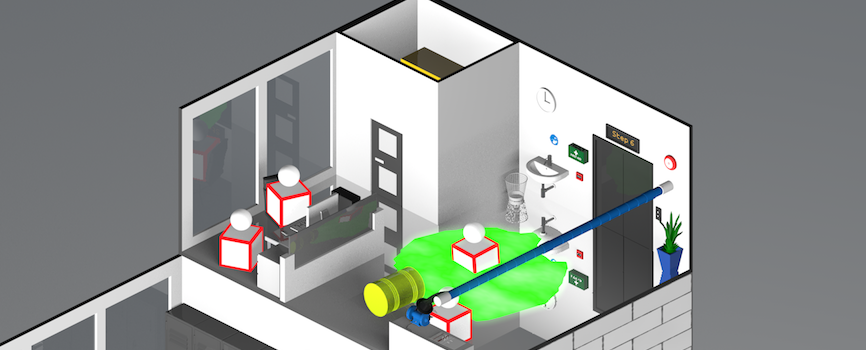
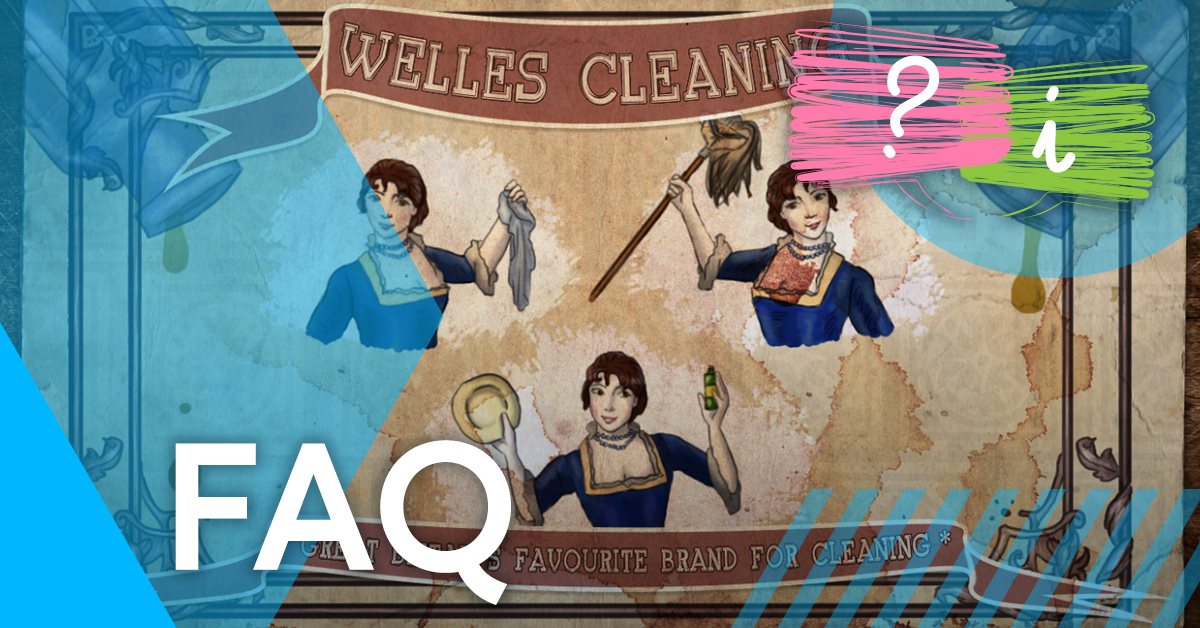
Opt-in to our newsletter
Receive industry news & offers